For the Colt Model 1911 type pistols by Les Bengston
Related tooling (available from Brownell’s, Inc.):
- Norton Fine India Stone (SN 657-246-246)
- Norton Hard Arkansas Stone (SN 657-300-650)
- Brownell’s Trigger Adjustment Pins .45 Auto (SN 080-622-001)
- Trigger Pull Scale (SN 747-094-500 or 747-873-070)
- The Colt .45 Automatic-A Shop Manual (SN 924-200-045)
- Hallock’s .45 Auto Handbook (SN 600-001-045)
Using the sear jig:
- Detail strip the frame and clean all parts thoroughly. Inspect all parts to ensure they are in good, unaltered condition. Parts that have been previously altered should be replaced with new factory or aftermarket parts.
- Use a fine India stone to lightly polish the hammer hooks. This can be done by placing the stone on a flat surface and holding the hammer hooks against it. Only a few strokes are necessary. Then mount the hammer in your bench vise with the area under the hammer hooks parallel to the top of the vise. Use a feeler gage to measure the height of the hooks. Opinions on the proper height of the hooks on a tuned hammer range from .018″ for bullseye competition guns to .026″ on duty guns. I use .024″ for duty/self defense/hunting/IPSC Limited guns. FOR COMPETITION USE ONLY you can reduce the hooks to .020″. To reduce the hook height, use the appropriate feeler gage leaf placed flat on the flat area below the hammer hooks. Then use you fine India stone to reduce he hammer hooks until the stone is just contacting the feeler gage.
- Install the sear on the sear jig using the position to cut the “de-creep” or “break away” angle, using the pistol’s sear pin to hold the sear on the jig. Opinion varies as to whether the depth of this cut should be 1/3 to 1/2 of the sear engagement area. I use the 1/3 figure on duty pistols and the 1/2 figure for competition only pistols. (The exact angle of the break away cut is not particularly important. Approximately 45 degrees is generally used.) Remove the sear from the jig and put Dykem or cold blue on the primary engagement surface.
- Install the sear on the jig using the position to cut the primary engagement angle, using the pistol’s sear pin to hold the sear on the jig. Hold the sear against the jig with your index finger. Make several passes against the fine India stone, inspecting carefully to ensure you are cutting with equal pressure on both sides of the sear engagement. Only remove a minimum of metal. Then remove the sear from the jig and clean it.
- Install the Brownell’s Trigger Adjustment Pins in the frame and put the hammer and sear on them. Inspect the hammer/sear engagement. The sear should be flat against the full cock notches of the hammer. If not, adjust the sear jig to cut the correct angle. If the front of the sear needs to be lowered, extend the jig screw. If the rear of the sear needs to be lowered, retract the jig screw. NOTE: Production tolerances vary between manufacturers. Tolerances also mean that exact angles required can vary from gun to gun. All sear jigs must be adjusted to each individual pistol to do a safe, effective trigger job. I use a Tasco 30X pocket microscope to examine the engagement angles of the hammer/sear and ensure they are correct.
- When the sear angle is correctly mated to the hammer, lightly stone the sides of the sear and the lower rear of the sear where the disconnector bears against it. Then stone the rear of the trigger where the disconnector bears and the rear and front of the disconnector. On the disconnector, also stone the flat where the trigger spring (three-leaf spring) bears. The top of the disconnector can be lightly polished where the slide rides on it.
- Clean all parts thoroughly, including the frame. Install the trigger in the frame and ensure that it moves freely. If not, the frame will have to have its trigger recesses polished lightly. When the trigger moves freely, lubricate it lightly and install the trigger and magazine catch. Install the sear, disconnector, trigger spring, hammer and mainspring housing. Check the trigger pull for crispness. Do not let the hammer fall fully to strike the frame. Use your thumb to catch it as it falls, but be careful not to catch your thumb between the ejector and hammer. It hurts and bleeding on a clients pistol is the mark of the non-professional. If the trigger pull is crisp, go on to step 8. If the trigger pull is not crisp, attempt to ascertain why. Disconnector click and engagement angles are both possibilities. Correcting the problem may be time consuming. Trigger jobs on .45s run less then an hour when all goes right to more than four hours when there are problems. I have never found an experienced professional who could determine exactly how long it will take on any particular pistol.
- When the trigger pull is crisp, install the upper assembly on the frame and put the front of the slide into the shop vise, using tape, leather or paper to ensure the vise jaws will not mark it. Then use your trigger pull scale to weigh the pull. If it is satisfactory, go on to step 9. If not, you will have to adjust the trigger spring to lower or raise the weight of pull. Disassemble the pistol, removing the upper assembly, the mainspring housing and trigger spring. Bend the left and center leafs of the spring towards the rear to lower the weight of pull and forwards to increase it. Hallock’s .45 Handbook contains a good illustration of the properly adjusted trigger spring which can be used as a starting point. Each pistol is different and will require slightly different spring configurations. When the springs have been bent, re-install the trigger spring and mainspring housing. Then check to ensure that the disconnector is held up to its full height. By pushing down on the top of the disconnector, you can ensure that it has proper tension. Re- install the upper assembly and again weigh the trigger pull. This is a trial and error process.
- When the trigger pull is correct, re-install the grip safety and thumb safety and check proper operation. Ensure that the trigger is not rubbing against the arm of the grip safety and altering the trigger pull. Then put the thumb safety in the on (up) position and try to pull the trigger while the grip safety is depressed. You should feel no trigger movement after the rear of the trigger and disconnector contact the sear. Then release the trigger, put your thumb between the rear of the slide and the front of the hammer and push the thumb safety to the off (lower) position. If you felt movement or the hammer dropped, you will have to adjust the thumb safety. This is done by lightly peening the engagement surface where the sear connects it. After peening, re-assemble and test again.
- After the trigger job, the pistol must be test fired. Start by loading a dummy round and a live round into the magazine. Chamber the live round, keeping the pistol pointed down range. Fire. The dummy round should have been chambered and the hammer remain at full cock. If the hammer remained at full cock, load a magazine with two live rounds and fire both. If no problems are encountered, load three rounds and fire. Then load a full magazine and fire it. I recommend that a full box of ammunition be fired through the pistol after a trigger job. REMEMBER, AN IMPROPERLY DONE TRIGGER JOB CAN RESULT IN UNCONTROLLABLE, FULL-AUTO FIRE. TAKE THE TIME TO ENSURE THAT THE JOB HAS BEEN DONE PROPERLY BEFORE RETURNING THE PISTOL TO A CLIENT.
- Weight of trigger pull is a subject of much discussion. Clients will often request very light trigger pulls. I will not put a trigger pull of less then 4 pounds on a duty/self defense pistol. With less experienced shooters a 4 1/2 pound pull is better and as high as 5 pounds is acceptable.
- FOR COMPETITION ONLY. When a client requests a lighter than 4 pound trigger pull, it should be on a competition only pistol. You should start with a competition grade after market hammer, sear, sear spring and trigger. The hammer hooks may be cut to .020.” The sear may have the break away angle take up to 1/2 of the top sear surface. An Ed Brown trigger spring (with the longer disconnector leaf) should be installed. All parts, including the trigger recess in the frame, should be well polished. In this manner, a light, crisp trigger pull may be obtained. While a trigger pull as light as 2 1/2 pounds may be had, I do not recommend going below 3 1/2 pounds except on pistols for experienced competitors. Any time you do a competition trigger job, the build sheet/work invoice should be clearly labeled, “FOR COMPETITION USE ONLY”
GENERAL NOTES:
On tuned triggers, the hammer can be jarred off full cock by dropping the slide with the slide stop due to trigger surge. (The inertia of the trigger allows it to travel backwards and bump the disconnector and sear slightly.) This is more apparent on very light trigger pulls. Various methods are used to control this problem, including holding the hammer back with the thumb while dropping the slide, holding the trigger to the rear while dropping the slide and cycling the slide with the non shooting hand rather than releasing the slide stop. The weight of the recoil spring being used will influence how hard the slide goes forward, with a heavier spring increasing the likelihood of trigger surge. You should make your client aware of this and discuss proper gun handling with him or her.
WARNING:
This sear jig is designed to be used by trained, qualified gunsmiths. Neither L. Bengtson Arms Company nor retailers of its products assume any liability for its incorrect use or damages resulting from such use.
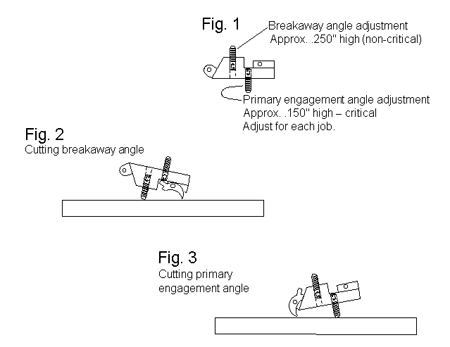
L. Bengtson Arms Company
Mesa, Arizona
(480) 981-6375
[email protected]
AAS in GUNSMITHING
CERTIFIED POLICE ARMORER
CERTIFIED GUNSMITHING INSTRUCTOR
Copyright © 1999 by L. Bengtson Arms Co.
Comments, suggestions, contributions? Let me know